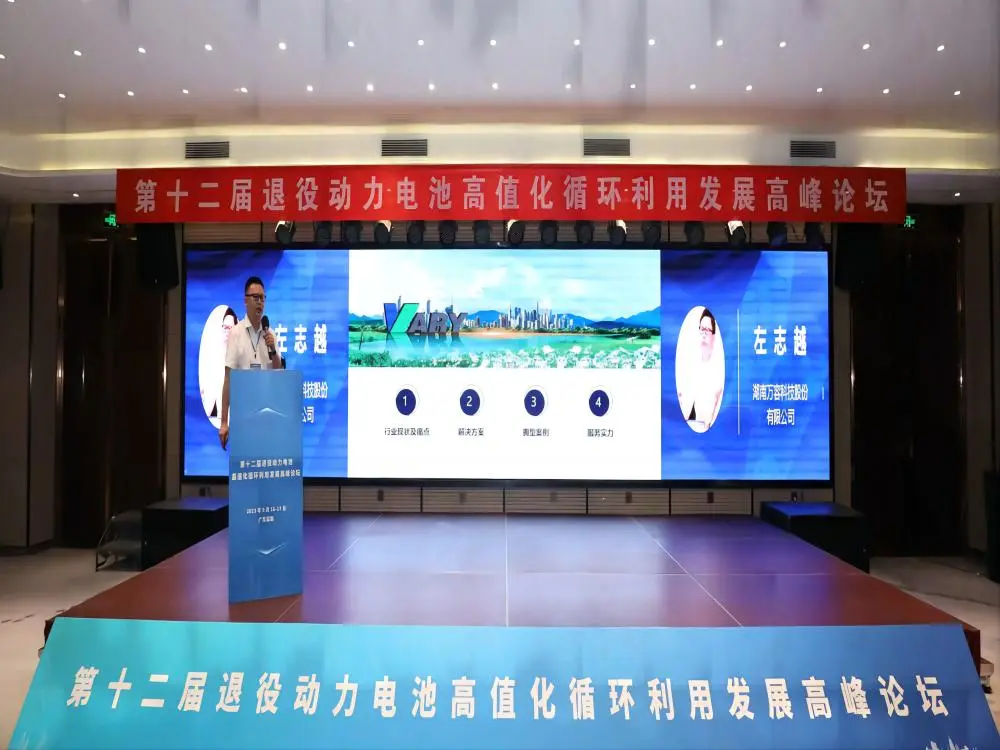
Lithium Battery Retirement Wave: This Enterprise Takes a Novel Approach to 'Curing' Lithium
With the rapid development of the new energy vehicle industry, the number of retired power batteries is increasing year by year, and how to achieve their high-value recycling has become a focus of industry attention. Serious leakage of electrolyte and electrode powder, the recycled positive electrode powder contains a large number of fine metal particles, the process is lengthy, and there are significant safety hazards. The drawbacks of traditional lithium battery recycling processes are apparent; is there a solution?
Hunan Vary Technology Co., Ltd. was invited to participate in the 12th Summit Forum on the High-Value Recycling and Development of Retired Power Batteries, providing a new solution for the comprehensive recycling and treatment of retired lithium batteries and battery industry waste. Chairman Ming Guoying was invited to host as a guest, and the director of the Research and Design Institute, Zuo Zhiyue, gave a keynote speech on "Technological Equipment and System Services for Recycling of Waste Lithium-ion Battery Materials."
Customers can choose integrated or segmented processing for retired lithium batteries based on factors such as production capacity, the diversity of waste lithium-ion battery materials, and front and back-end production matching. They can choose equipment combinations such as shredding, pyrolysis, and sorting to achieve the safe and environmentally friendly recovery of all components of retired lithium batteries, including copper foil, aluminum foil, and electrolyte, with no membrane by-products throughout the process. The recovery rate of electrode powder is high. Compared to low-temperature drying or volatile processes, the pyrolysis process stabilizes the ternary electrode powder, with no spontaneous heating, ensuring high safety. In terms of the overall process, screening is reduced compared to traditional processes, making maintenance simple and efficient.
What to do with completely scrapped lithium batteries, including electrode sheets, membranes, and the waste slurry produced during production? "This is our scrapped electrode physical recovery production line in Miluo, and we have achieved a recovery rate of ≥99% for black powder. For this project, we upgraded in terms of operating costs, streamlining the process, and input methods. We adopted a two-stage crushing integrated machine, screening, vortex crushing and grading process, minimizing the use of screening to avoid problems such as easy damage and difficult maintenance in the multi-stage screening process." Director Zuo introduced the company's case, "For scrapped electrode sheets, membranes, and waste slurry, we can also use pyrolysis for recovery. The recovery rate of electrode powder from scrapped electrode sheets is higher through pyrolysis, with aluminum content less than 500 ppm, and battery slurry pyrolysis can achieve the recycling of NMP. Considering the scrapped electrode sheets, membranes, and waste slurry produced by many battery production enterprises themselves, we can provide in-house cooperation models. In addition, for the recovered ternary electrode powder, we can also provide reduction roasting, which can achieve precise temperature control, automatic production line control, and high production efficiency." Currently, Vary Technology's waste lithium-ion battery material recycling technology and equipment have been applied to multiple projects in Hunan and Jiangxi.
According to statistical predictions, the global battery recycling market space will exceed 150 billion yuan by 2027, and the track of power battery recycling will attract more companies to enter. Vary Technology will continue to focus on research and development, promote the industrial operation of waste lithium-ion battery material recycling technology and equipment, enhance the efficient reuse of lithium-ion battery materials, and contribute technological strength to the industry's resourceization, high value, and green development.